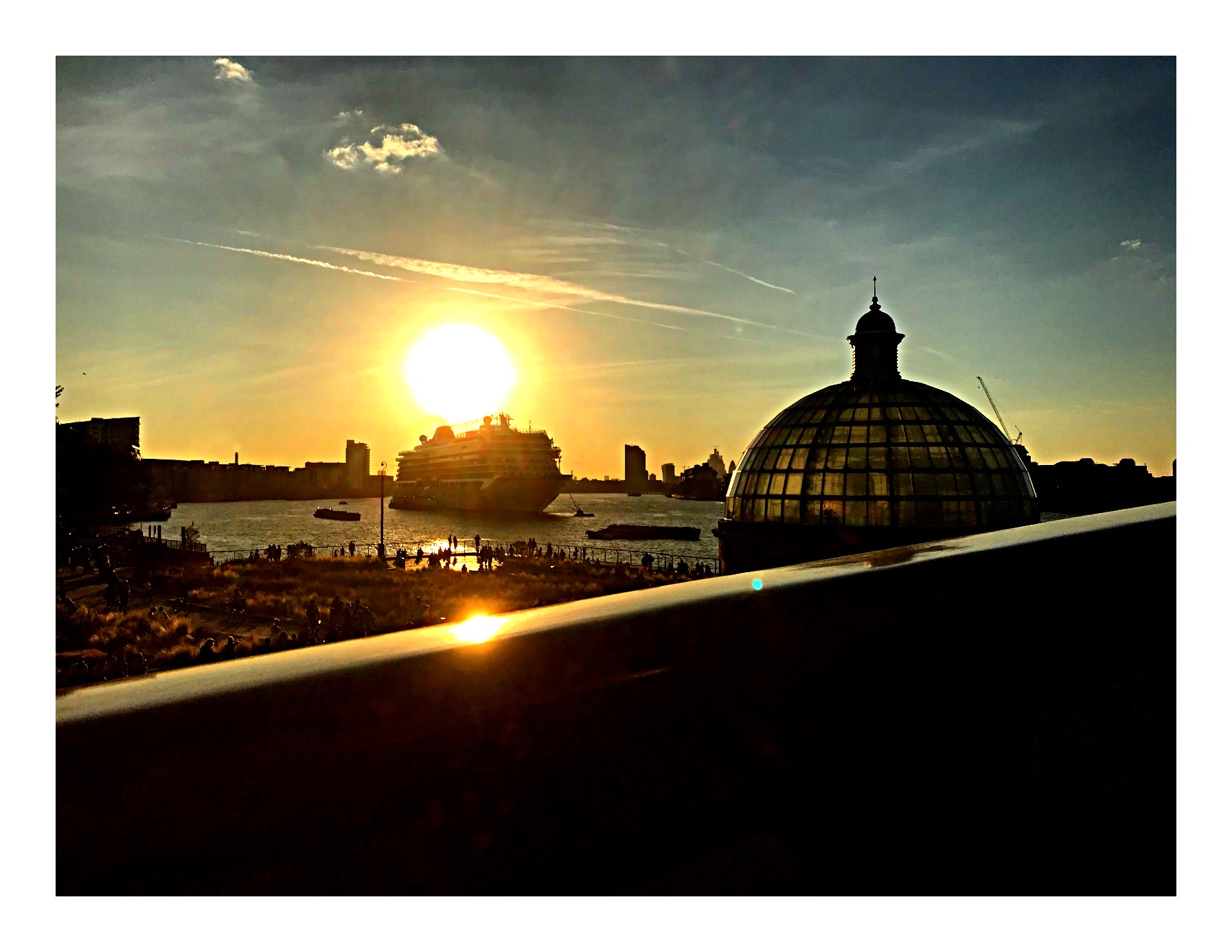
At AVIANNEGREEN.COM Ltd., our mission is to turn your dreams and aspirations into reality. We are only limited by your imagination.

AVIANNEGREEN.com | OEM Manufacturing Services
Have you ever dreamed of creating your own brand of products? With over 60 years of experience in manufacturing and a network of trusted partners worldwide, we can turn your vision into reality. Let us help bring your ideas to life.